On-Demand Packaging Equipment Service to Assistance Your Production Requirements
On-Demand Packaging Equipment Service to Assistance Your Production Requirements
Blog Article
Expert Product Packaging Tools Service for Seamless Procedures
In today's hectic manufacturing atmospheres, the significance of skilled product packaging devices service can not be underrated. The landscape of devices service is evolving, providing both challenges and chances that call for additional expedition.
Value of Expert Solution
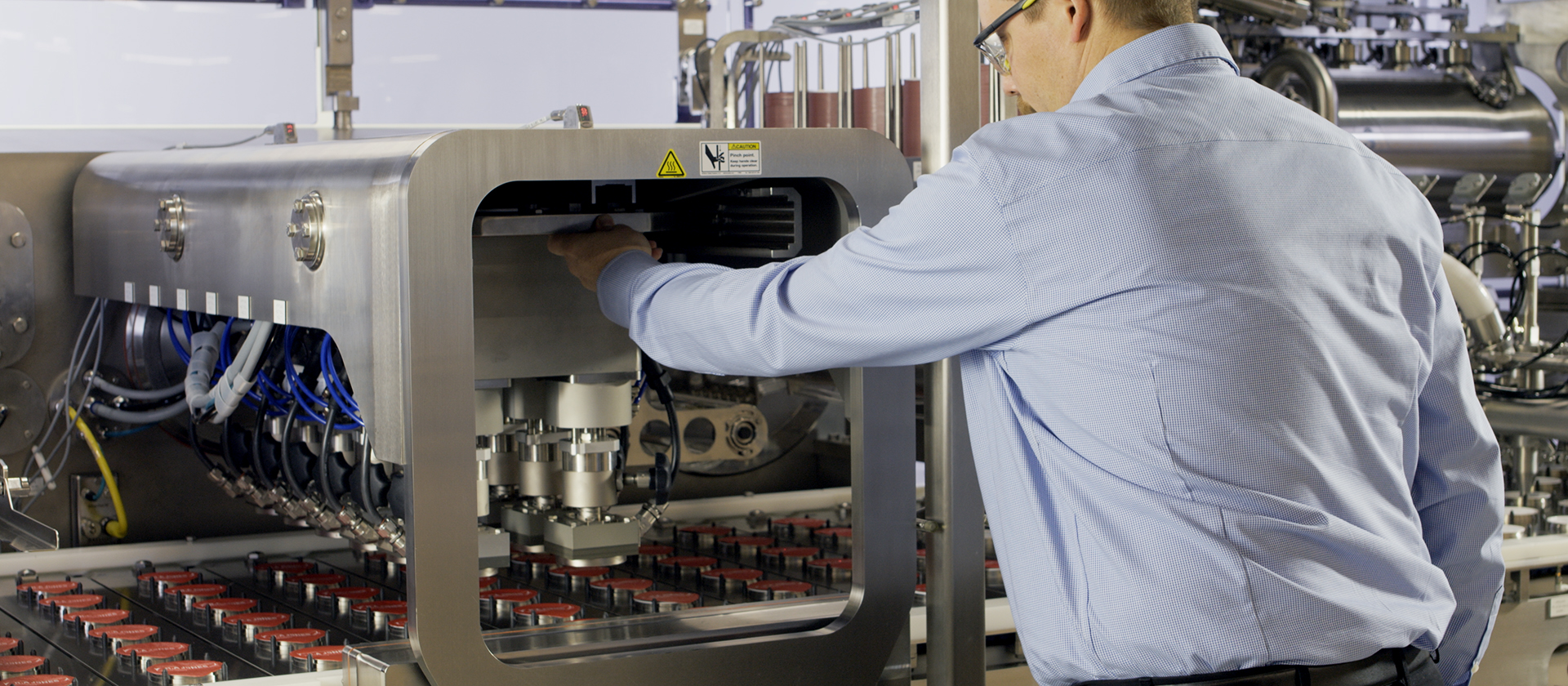
Moreover, routine maintenance by specialists helps lengthen the lifespan of packaging devices. Professional solution suppliers are furnished with comprehensive understanding of numerous equipment kinds and sector criteria, enabling them to execute preventative upkeep properly. This aggressive strategy not only decreases the probability of unpredicted breakdowns but also enhances general operational reliability.
Additionally, experienced service can dramatically contribute to compliance with governing standards. Product packaging devices need to follow stringent safety and high quality guidelines, and expert specialists make certain that these criteria are satisfied continually. This not just safeguards product stability but likewise safeguards the company's credibility.
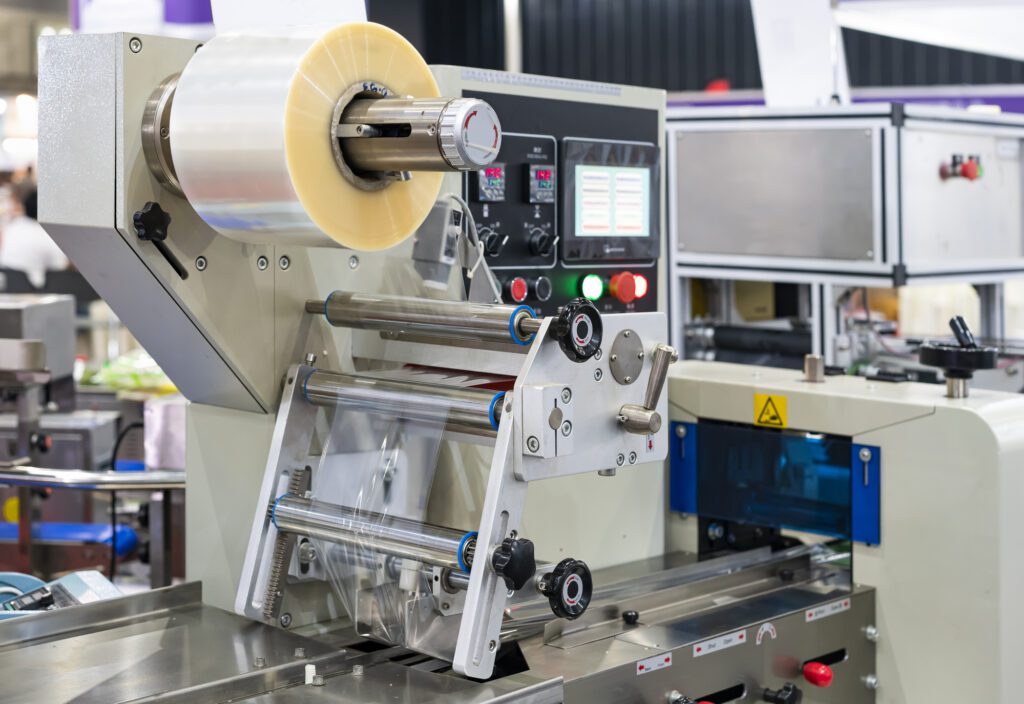
Benefits of Expert Assistance
Engaging specialist support for packaging devices not only boosts functional efficiency yet additionally provides an array of fringe benefits that can significantly influence a company's profits. One of the most noteworthy benefits is the reduction of downtime. Expert service technicians can quickly diagnose and fix problems, guaranteeing that manufacturing lines remain energetic and reducing the monetary losses linked with idle equipment.
Moreover, expert support frequently consists of preventative maintenance, which can expand the lifespan of product packaging equipment. By routinely servicing equipment, prospective issues can be determined and attended to before they escalate right into pricey fixings or replacements. This positive method not only saves cash but additionally boosts product high quality by guaranteeing that tools operates within optimal parameters.
Furthermore, leveraging the experience of experienced experts can bring about enhanced conformity with industry laws. These professionals stay upgraded on the most current standards and can direct companies in executing best techniques, consequently preventing potential lawful liabilities.
Sorts Of Packaging Equipment Provider
When it comes to packaging tools solutions, services can select from a variety of choices customized to meet their specific requirements. These solutions typically drop right into several classifications, each created to boost operational efficiency and lessen downtime.
Preventative maintenance services concentrate on regular assessments and upkeep tasks to ensure that devices runs smoothly and decreases the chance of unanticipated break downs. This proactive approach can extend the lifespan of machinery and improve productivity.
Repair services are important for addressing tools breakdowns or failings - packaging equipment service. Experienced specialists identify the problems and do essential repairs, ensuring that the machinery is recovered to optimum working conditions without delay
Installation services are essential when presenting brand-new product packaging devices. Experts deal with the setup, ensuring that the equipment is integrated properly into existing lines and functions as meant.
Educating services provide team with the required skills and understanding to operate equipment efficiently. This training can cover every little thing from try this out standard operation to advanced troubleshooting.
Last but not least, speaking with services offer critical insights right into optimizing product packaging processes, helping organizations determine locations for enhancement and implement best techniques. Overall, selecting the appropriate combination of these solutions can dramatically enhance packaging operations.
Key Attributes to Seek
What essential characteristics should businesses take into consideration when choosing packaging equipment solutions? Furthermore, the availability of thorough support solutions, including installment, upkeep, and troubleshooting, makes sure that organizations can depend on prompt support when issues emerge.
One more key attribute is the versatility of service offerings. A service provider that can adjust to developing service needs, such as changes in production read here quantity or product packaging specifications, will contribute in keeping effectiveness. Innovation assimilation should be a top priority; modern-day product packaging equipment services need to incorporate sophisticated innovations, such as automation and real-time tracking, to improve efficiency.
Finally, online reputation and customer responses need to not be ignored. Engaging with endorsements and situation studies can provide a clearer image of a service supplier's integrity and top quality. By considering these important attributes, services can make informed choices that will sustain their product packaging procedures and add to general success.
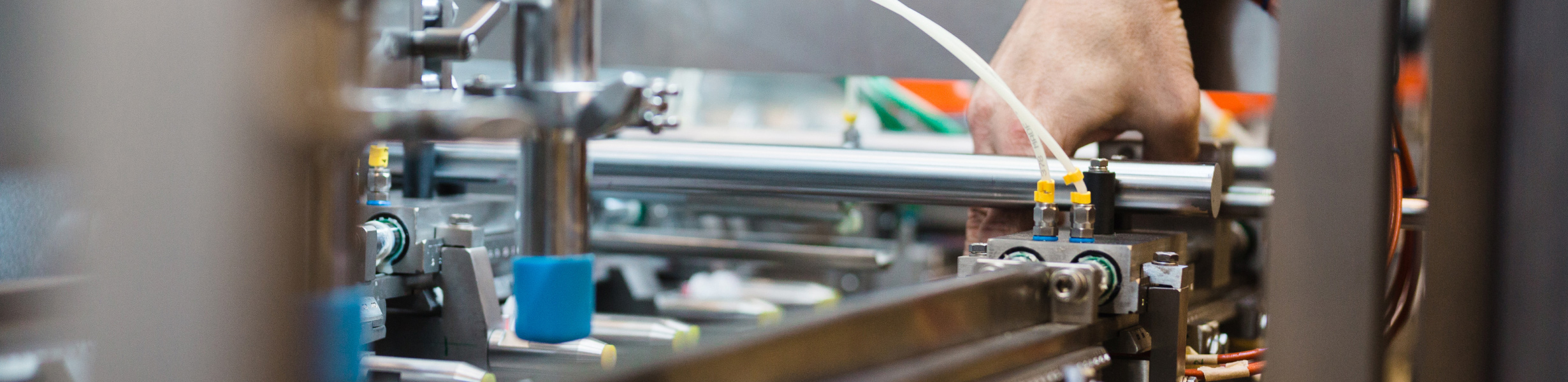
Buying Long-Term Success
Spending in lasting success in product packaging equipment services needs a tactical approach that focuses on sustainability and scalability. Business should concentrate on choose devices that not just satisfies current operational needs my response however also suits future growth and technical advancements. This insight minimizes disruptions and boosts general effectiveness.
An essential part of this financial investment is the regular maintenance and service of equipment. Developing a positive solution schedule minimizes downtime and prolongs the life-span of machinery, eventually resulting in set you back savings. Partnering with professional company guarantees that the tools is maximized for performance, therefore preserving high manufacturing requirements.
Moreover, integrating innovative technologies, such as automation and IoT connection, can dramatically improve functional capabilities. These developments enable for real-time tracking and data analysis, enabling companies to make educated decisions that line up with their long-lasting objectives.
Last but not least, purchasing employee training on new innovation and best practices promotes a culture of continual improvement. By growing a competent workforce, organizations can adapt to altering market needs and preserve their one-upmanship. Inevitably, an all natural technique that includes equipment, solution, innovation, and workforce development placements firms for sustained success in the product packaging industry.
Conclusion
In verdict, expert packaging tools solution plays an essential duty in making certain smooth procedures within manufacturing atmospheres. By focusing on these services, businesses can accomplish optimum functional efficiency and extend the life expectancy of their equipment.
Report this page